It would be lovely...
It would be lovely...
to see some more active CAM stuff...because I'm selfish. Somehow I was moved from my design only position to something closer to "Continuous improvement". My first big continuous improvement is to attempt to reorganizing the wreak of a programming system we have here to something more resembling what a company with multiple millions in sales should look like rather than what might result from "Bob" attempting to print out a various repair parts for his remote controlled airplane in his garage.
Re: It would be lovely...
My personal experience in CAM is pretty narrow, but I'd love to see more CAM related stuff, and in particular what CAD people can do to make CAM work better and give better results. Maybe you could start out by writing something about that? What sorts of things do CAD operators do that make you want to bust a monitor over someone's head?
Blog: http://dezignstuff.com
- Frederick_Law
- Posts: 1944
- Joined: Mon Mar 08, 2021 1:09 pm
- Location: Toronto
- x 1634
- x 1467
Re: It would be lovely...
Like 0.06" rad on all internal and external corners?
Re: It would be lovely...
ALL CAD people should have a working knowledge of manufacturing prior to ever being allowed to release something to manufacture.matt wrote: ↑Mon Mar 08, 2021 4:03 pm My personal experience in CAM is pretty narrow, but I'd love to see more CAM related stuff, and in particular what CAD people can do to make CAM work better and give better results. Maybe you could start out by writing something about that? What sorts of things do CAD operators do that make you want to bust a monitor over someone's head?
The list of things that "CAD" people do to make parts more difficult, more expensive or just down right impossible to make is fairly endless.
Re: It would be lovely...
Well, then that sounds like a great place to start a great discussion. Educate some CAD users!

Blog: http://dezignstuff.com
Re: It would be lovely...
I programmed and help make a part out of a solid chunk of 316SS. Hard to describe but it had .03-.06 rad essentially everywhere there was a corner. The part had a bunch of "Ears" on it that formed a pocket of sorts. In one area the shortest reach we had to get to the corner from any direction was 3 1/2 inches. It was a military aerospace part and the customer refused to change the radius despite the fact it could have been 1/2" rad. That was fun.....06" radius in 316SS with a 4" tool. We ended up making special extensions and breaking a whole lot of tools.
Re: It would be lovely...
Here's a few
1) Always think "How is that going to be made?" If you don't know how to make don't design it or find someone that might actually know if it can be made.
2) Watch your reaches. Making a feature that needs a 1/8" end mill to make and you can only reach it with a 10" long tool is bad, very bad.
3) Ask yourself "Do I REALLY need"
a) ALL those threads?
b) That tight of tolerance
c) All those radii
4) How many setups - Goes back to "How and I going to make this". If you can make a part that works with features on three sides....don't put features on four sides.
5) "Pretty" is expensive.
6) Pay attention to materials. Making a part out of a tougher material may be necessary, but if it really isn't you just double the cost of your part.
7) You can't ever have enough information on the drawing. No one ever walked into my office, plopped down a drawing and said "Dude there is absolutely everything I need on this print to make the part and then some". A view takes seconds to add in a CAD system, ADD THEM. Notes, dimensions, reference dimensions, more views. Make the views clear, large enough for an old 60 year old machinist to see and understand.
8) Fancy is expensive. Don't over design something because you're being clever and putting that expensive engineering degree to work. If a block with four holes fits the design requirements, don't turn it into something else to make it "Better".
9) Know enough about making parts so that when you're done with the part the person making the part can look at the drawing and know how you want it made.
For a start....
Re: It would be lovely...
I've made lists like this for designing plastic parts. Some of the plastic manufacturing process goes through the machine shop. Sometimes it's hard to think that far ahead - thinking of the part design and function plus the mold and the mold making process. It can be a lot to think about all at once, but it comes with experience, and usually with the memory of a red-faced machinist yelling some unintelligible at you before you can sit down at your desk in the morning. It's good to hear what other people need, though.
Blog: http://dezignstuff.com
Re: It would be lovely...
I worked in production before i started to learn SW. That is most helpful thing i have today while designing 
Also , i really try to have good communication with our production , and i am not ashamed to ask questions what is easier for them to make.

Also , i really try to have good communication with our production , and i am not ashamed to ask questions what is easier for them to make.
-
- Posts: 1
- Joined: Tue Mar 09, 2021 3:52 am
- x 1
Re: It would be lovely...
Amen to all of the points in this thread so far; I used to train new "Essentials" users on Inventor and by far the best users were those who had previous machining experience.
In one class in particular, I had a CNC machinist sat alongside a Mechanical Engineering under-graduate and when I mentioned ISO Limits/fits & Tolerances all I got was a blank stare from the University chap.
One point I would add is this:
Specify fewer bolts; a standard 5mm bolt can support a 1000kg mass. In fact, the material the bolt is attached to is likely to fail before the bolt does.
PS. if you ever wonder why Herman Miller chairs are so expensive, it's because a) they make great chairs but also:
In one class in particular, I had a CNC machinist sat alongside a Mechanical Engineering under-graduate and when I mentioned ISO Limits/fits & Tolerances all I got was a blank stare from the University chap.
One point I would add is this:
Specify fewer bolts; a standard 5mm bolt can support a 1000kg mass. In fact, the material the bolt is attached to is likely to fail before the bolt does.
PS. if you ever wonder why Herman Miller chairs are so expensive, it's because a) they make great chairs but also:
(I know because I had to clean their CAD models for use in CET Designer - man that was painful)
- Tony Tieuli
- Posts: 23
- Joined: Mon Mar 08, 2021 3:22 pm
- Location: Massachusetts, USA
- x 446
- x 64
Re: It would be lovely...
That's an excellent start!MJuric wrote: ↑Mon Mar 08, 2021 4:57 pmHere's a few
1) Always think "How is that going to be made?" If you don't know how to make don't design it or find someone that might actually know if it can be made.
2) Watch your reaches. Making a feature that needs a 1/8" end mill to make and you can only reach it with a 10" long tool is bad, very bad.
3) Ask yourself "Do I REALLY need"
a) ALL those threads?
b) That tight of tolerance
c) All those radii
4) How many setups - Goes back to "How and I going to make this". If you can make a part that works with features on three sides....don't put features on four sides.
5) "Pretty" is expensive.
6) Pay attention to materials. Making a part out of a tougher material may be necessary, but if it really isn't you just double the cost of your part.
7) You can't ever have enough information on the drawing. No one ever walked into my office, plopped down a drawing and said "Dude there is absolutely everything I need on this print to make the part and then some". A view takes seconds to add in a CAD system, ADD THEM. Notes, dimensions, reference dimensions, more views. Make the views clear, large enough for an old 60 year old machinist to see and understand.
8) Fancy is expensive. Don't over design something because you're being clever and putting that expensive engineering degree to work. If a block with four holes fits the design requirements, don't turn it into something else to make it "Better".
9) Know enough about making parts so that when you're done with the part the person making the part can look at the drawing and know how you want it made.
For a start....
One thing I would add right off the top of my head is to dimension your model to the mean of the tolerance. Most CAM programmers who use the model, create their toolpaths right on the model. If the dimension is 1.000 +.010 / -.000, model it at 1.005. When you model it to the high or low the CAM programmer has to make changes to get the toolpath on the mean. Yes, you can have the machinist on the shop floor use offsets to get the part on the mean but I prefer to give them a clean program.
-
- Posts: 423
- Joined: Tue Mar 09, 2021 10:11 am
- x 439
- x 233
Re: It would be lovely...
Does a plasma count as CAM too?
Re: It would be lovely...
Sure. Plasma, waterjet, laser... all CNC driven.
Blog: http://dezignstuff.com
- mike miller
- Posts: 878
- Joined: Fri Mar 12, 2021 3:38 pm
- Location: Michigan
- x 1070
- x 1231
- Contact:
Re: It would be lovely...
That's a great list @MJuric .
I frequently run out to the floor and measure tools to see if we have a certain size drill already in stock, or if a standard ER32 toolholder will clear a sidewall, or if a standard tap will reach XX deep, or what the corner rad is on CCMT32.50.5 inserts....you get the idea. An engineer who has no experience in machining or doesn't bother checking tooling capabilities will make life very miserable for the machining dept.
I frequently run out to the floor and measure tools to see if we have a certain size drill already in stock, or if a standard ER32 toolholder will clear a sidewall, or if a standard tap will reach XX deep, or what the corner rad is on CCMT32.50.5 inserts....you get the idea. An engineer who has no experience in machining or doesn't bother checking tooling capabilities will make life very miserable for the machining dept.
He that finds his life will lose it, and he who loses his life for [Christ's] sake will find it. Matt. 10:39
Re: It would be lovely...
And nothing ruins your day quite like having and angry, smelly, likely hung over grumpy old machinist standing over your shoulder foaming at the mouth and teeth grinding all because they broke off a tap in a part because you made them use some ungodly length tool or tool extension.mike miller wrote: ↑Fri Mar 12, 2021 4:59 pm That's a great list @MJuric .
I frequently run out to the floor and measure tools to see if we have a certain size drill already in stock, or if a standard ER32 toolholder will clear a sidewall, or if a standard tap will reach XX deep, or what the corner rad is on CCMT32.50.5 inserts....you get the idea. An engineer who has no experience in machining or doesn't bother checking tooling capabilities will make life very miserable for the machining dept.
One of the things we used to do to machinist was create a "Scrap tree". We'd hang a chain off their machine and every part they scrapped we'd tac weld it to the chain. To this day I keep a well stocked pile of "things I screwed up recently" on my desk as a reminder to pay attention to what I'm doing.
- Glenn Schroeder
- Posts: 1518
- Joined: Mon Mar 08, 2021 11:43 am
- Location: southeast Texas
- x 1755
- x 2126
Re: It would be lovely...
I'm afraid I don't know anything about CAM, but I could go on for hours about engineers with no practical experience designing things that are much more complicated than they need to be to achieve the goal, spec a material that's only made in limited quantities on February 29th, or call out rebar bent to 1/16" tolerance.
"On the days when I keep my gratitude higher than my expectations, well, I have really good days."
Ray Wylie Hubbard in his song "Mother Blues"
Ray Wylie Hubbard in his song "Mother Blues"
Re: It would be lovely...
This is actually quite a challenge for me when designing machines. On one end of the spectrum you're designing something like a spindle where tolerances reach down into the .000X" range and sometimes less. Then you switch to the enclosure and you drop a tolerance down that is +/-.03 and you think you're giving all the tolerance in the world.
I always have stop, switch gears and realize that I'm now dealing with a guy at a break press using scribe lines not a highly accurate machine with glass scales and linear rails. That guy is NEVER going to be able to make four bends on two parts and have them fit inside of each other +/- .06"...not going to happen. Well maybe it might, but it would be more luck than being able to hold tolerances.
Another challenge I run into is one of scale. At one time I was working on two different projects at the same time. One was a desktop unit with eight lanes that processed chemicals and media for the medical industry. LOTS going on in a tiny area. At the same time I was working on a project that filled three stories of a building. In one I would drop an M16 bolt in and it would be WAY to small. I'd then switch over to the other and drop in an M8 and it's cover half the screen :-)
Re: It would be lovely...
Or call out surface flatness 0,1mm on sheet plate 1000x1000mm ,1mm thick, becase "i need this side to be flat".

Re: It would be lovely...
Re: It would be lovely...
You really boiled my blood ,than i had a click for font colour
Re: It would be lovely...
Yes, for the most part the complete loss of knowledge about actual manufacturing is resulting in most "Designers" and "Engineers" simply CYA'ing and dropping tiny tolerances on everything. Then everyone wonders how it's possible that a plate with four tapped holes cost us $8000 dollars. Well you had a material called out that required a special pour at the foundry, you had a flatness callout that required we send it thru several processes down to a lapping to a mirror finish, you're heat treat call out was a five step process and then you plated it with gold...
At one point manufacturers would have thrown a flag on this stuff. Today it happens so often that they just do it knowing that it's going to cost an arm and a leg and knowing that a prox bracket holder is not going to the moon despite being designed like it is.
Re: It would be lovely...
It's a vicious cycle. One problem with CAM becoming so accessible is that you now have too many *machinists* these days who don't really understand much beyond programming, the same way you now have too many QC techs who can program a CMM, but have never acquired the ability to judge workmanship just from holding a part and running their fingertips over it. The end result is a universal overconfidence in the computer side of the process and a tendency to view tolerances as "tight" or "forgiving" only based on their numerical value, rather than connecting them to the setups and steps needed to achieve them.
So yes, I will sometimes put in a WTF tolerance in order to force a dialogue on the point and get people to think *before* the machine tool starts running.
So yes, I will sometimes put in a WTF tolerance in order to force a dialogue on the point and get people to think *before* the machine tool starts running.
Re: It would be lovely...
Yes. One-sided tolerancing is equivalent in many ways to manual override of drawing dimensions and should be punished by flogging.Tony Tieuli wrote: ↑Thu Mar 11, 2021 11:52 am
That's an excellent start!
One thing I would add right off the top of my head is to dimension your model to the mean of the tolerance. Most CAM programmers who use the model, create their toolpaths right on the model. If the dimension is 1.000 +.010 / -.000, model it at 1.005. When you model it to the high or low the CAM programmer has to make changes to get the toolpath on the mean. Yes, you can have the machinist on the shop floor use offsets to get the part on the mean but I prefer to give them a clean program.
Re: It would be lovely...
How would the designer know how the process varies from nominal? What you're saying means that the designer needs to know that the process varies symmetrically. How would one convey design intent that says I want 1.00", can go over but do not go under?Jim Elias wrote: ↑Mon Apr 05, 2021 5:48 amYes. One-sided tolerancing is equivalent in many ways to manual override of drawing dimensions and should be punished by flogging.Tony Tieuli wrote: ↑Thu Mar 11, 2021 11:52 am
That's an excellent start!
One thing I would add right off the top of my head is to dimension your model to the mean of the tolerance. Most CAM programmers who use the model, create their toolpaths right on the model. If the dimension is 1.000 +.010 / -.000, model it at 1.005. When you model it to the high or low the CAM programmer has to make changes to get the toolpath on the mean. Yes, you can have the machinist on the shop floor use offsets to get the part on the mean but I prefer to give them a clean program.
1.00" +0.010" -0.000" is certainly not the same as 1.005" +-0.005
- mattpeneguy
- Posts: 1386
- Joined: Tue Mar 09, 2021 11:14 am
- x 2489
- x 1899
Re: It would be lovely...
Hey @matt,
Is there a setting somewhere to make it to where anything @Frederick_Law posts defaults to the sarcasm purple?
Re: It would be lovely...
In my line, the prevailing school of thought says that process and design intent get discussed with manufacturing and recorded with explication, while numerical tolerancing on dimensions tell the conditions that need to be fulfilled in order to have a functional part, no more and no less. So in my world, the two expressions you give are indeed equivalent.bnemec wrote: ↑Mon Apr 05, 2021 12:13 pm
How would the designer know how the process varies from nominal? What you're saying means that the designer needs to know that the process varies symmetrically. How would one convey design intent that says I want 1.00", can go over but do not go under?
1.00" +0.010" -0.000" is certainly not the same as 1.005" +-0.005
But my beef with one-sided tolerancing on drawings isn't about being a preacher for a particular way of thinking/communicating, but rather because it necessitates a ton more offline analysis due to there being no feedback in the 3-D design environment.
Re: It would be lovely...
From a machinist point of view it is. If you give me a dimensions of 1.00 +/.01 or 1.005 +/-.005, I'm going to shoot for 1.005 in both cases. There are some exceptions to this, say dies where if this was a hole they would shoot for 1.010, because as the punch wears the hole will get smaller.
The only way to get "Closer" to a dimension is by making the tolerance tighter.
Now that being said what do you design for features that are either "MAX" or "MIN"? If I have a .060R "MIN" inner radius, what should I model that too? It can be no smaller than .06 but I don't care if it's 2.000 or 200.
All that being said I do not think that not using "Nominal all the time in all situations" is necessary or even good design practice in some cases. I think this is particularly true in situations where you have standard fits and tolerances. If I'm going to call out an H6 fit on a hole I'm not including half the tolerance to the model because the H6 fit is -0/+X. Almost all the tolerances in the ISO system are unidirectional. Many are even +/+ and -/-. This is done this way for the express purpose that most people don't design to nominal, so that the numbers are rounded.
I can model a 40mm hole and put G7 tolerance on it and it's +.009mm/+.025mm. I don't model to 40.017mm for several reason. First you would then have to modify the dim in order to get it to read 40mm in order to get the right fit and second you're far less likely to screw up when designing around 40mm then you are when you are designing around 40.017. Clean round numbers work best for a number of reasons.
From the programming side, yep, its way easier to work with a model that is nominal, but working toward the nominal from a unilateral is not all that difficult in most cases.
Re: It would be lovely...
I could make it all invisiblemattpeneguy wrote: ↑Mon Apr 05, 2021 12:28 pmHey @matt,
Is there a setting somewhere to make it to where anything @Frederick_Law posts defaults to the sarcasm purple?

Blog: http://dezignstuff.com
Re: It would be lovely...
I had a junior engineer that was too arrogant and lazy to avail himself of the machine shop just outside our area. In reviewing one of his models I immediately saw things that just weren't going to fly. It was a plastic part but it straight sides and sharp corners and was modeled more like a simple machined part. I asked him about the draft and he said "Oh, I'm leaving that up to the mold maker." Okay, how about the parting line, where will that be? "Oh, I'm leaving that up to the mold maker too." Uh-huh. Where will the gate go? "What's that?" I asked if I could use his mouse for a few minutes and then quickly put in some draft, which naturally also determined the parting line. I put in a pocket for the gate and added some radii where it would be. His jaw just dropped and he said "That won't work with the other parts!" But he quickly realized it was his error in not knowing about these things.
The moral of this story is "You have to understand the process you are inherently specifying or else you are nothing more than a cartoonist." Okay, a 3-D cartoonist.
The moral of this story is "You have to understand the process you are inherently specifying or else you are nothing more than a cartoonist." Okay, a 3-D cartoonist.
Brick walls are there for a reason. The brick walls aren't there to keep us out. The brick walls are there to show us how badly we want things.
- - -Randy Pausch
- - -Randy Pausch
Re: It would be lovely...
Not quite. The first thing any part manufacturer wants to know is: what is scrap and what's not scrap (i.e. what can be billed for). That's what the drawing tolerance dictates in unambiguous fashion.MJuric wrote: ↑Mon Apr 05, 2021 12:54 pmFrom a machinist point of view it is. If you give me a dimensions of 1.00 +/.01 or 1.005 +/-.005, I'm going to shoot for 1.005 in both cases. There are some exceptions to this, say dies where if this was a hole they would shoot for 1.010, because as the punch wears the hole will get smaller.
The only way to get "Closer" to a dimension is by making the tolerance tighter.
There is room to negotiate after that without needing to make that tolerance tighter. It may be that assembly requires less individual fitting if the actual tends toward limit rather than mid-tolerance, etc. But those are things that really merit detailed discussions covering both the commercial and technical aspects of the doing, and the results of those discussions belong on the work order or PO rather than the drawing.
ISO fits are indeed the usual exception to the "middle of tolerance" rule, although most shops will appreciate it if the ISO fits as well have been moved to middle of tolerance in the models they get for CAM. (There are plenty of macros out there for this.) Even so, I now avoid using/citing them in cases where there isn't a long-standing historical precedent for a defined use case, such as H7 being a transition fit for a metric dowel pin. A tolerance I choose may be identical to 40G7, but on my drawing it will say 40.025/40.009, and although I generally agree with the "clean round numbers" principle during the designing, the final archived model after the job is finished will have 40.017. It used to be that machinists and designers could immediately visualize the approximate tolerance field based on the designation, and it's just not that way any more.MJuric wrote: ↑Mon Apr 05, 2021 12:54 pm
Now that being said what do you design for features that are either "MAX" or "MIN"? If I have a .060R "MIN" inner radius, what should I model that too? It can be no smaller than .06 but I don't care if it's 2.000 or 200.
All that being said I do not think that not using "Nominal all the time in all situations" is necessary or even good design practice in some cases. I think this is particularly true in situations where you have standard fits and tolerances. If I'm going to call out an H6 fit on a hole I'm not including half the tolerance to the model because the H6 fit is -0/+X. Almost all the tolerances in the ISO system are unidirectional. Many are even +/+ and -/-. This is done this way for the express purpose that most people don't design to nominal, so that the numbers are rounded.
I can model a 40mm hole and put G7 tolerance on it and it's +.009mm/+.025mm. I don't model to 40.017mm for several reason. First you would then have to modify the dim in order to get it to read 40mm in order to get the right fit and second you're far less likely to screw up when designing around 40mm then you are when you are designing around 40.017. Clean round numbers work best for a number of reasons.
From the programming side, yep, its way easier to work with a model that is nominal, but working toward the nominal from a unilateral is not all that difficult in most cases.
Re: It would be lovely...
You know, in theory, of course, you're right. But I'm a pretty experienced plastics design guy, and when it's not really obvious, I do leave it to the mold guys. Especially if there is a core pull or something, and the mating surfaces aren't called out on a drawing. Generally, I consult with the mold maker and then model the draft explicitly, but as a plastic part designer, I'm not going to tell the molder how to design his mold. There are all sorts of things plastic part designers don't think about that the mold maker needs to determine:DennisD wrote: ↑Mon Apr 05, 2021 2:01 pm I had a junior engineer that was too arrogant and lazy to avail himself of the machine shop just outside our area. In reviewing one of his models I immediately saw things that just weren't going to fly. It was a plastic part but it straight sides and sharp corners and was modeled more like a simple machined part. I asked him about the draft and he said "Oh, I'm leaving that up to the mold maker." Okay, how about the parting line, where will that be? "Oh, I'm leaving that up to the mold maker too." Uh-huh. Where will the gate go? "What's that?" I asked if I could use his mouse for a few minutes and then quickly put in some draft, which naturally also determined the parting line. I put in a pocket for the gate and added some radii where it would be. His jaw just dropped and he said "That won't work with the other parts!" But he quickly realized it was his error in not knowing about these things.
The moral of this story is "You have to understand the process you are inherently specifying or else you are nothing more than a cartoonist." Okay, a 3-D cartoonist.
- how to get the part out of the mold.
- which side does the part stick to
- knit lines on cosmetic surfaces
- knife edges in the mold
- ejector pins
- mold cooling
- bubbler pins inserts
Otherwise, I'd be designing collapsing cores for every part because I can. Or overmolds because they're easy. Or specify structural foam process because it allows me thick walls or one of a couple dozen other mistakes that rookies who don't think they're rookies make that a mold designer doesn't make. He knows which parts are expensive or hard to machine or wear out fast, or a part that's in this catalogue but not that one.
There's nothing quite as miserable as removing draft and fillets and then redoing them with the correct scheme.
It's so easy for a plastics designer to double the cost of the mold just by not knowing that the shrink will pull away from some surfaces but on to others. Or that you might be able to allow a thick section with a bubbler, but is that really possible where you want it?
Don't throw it over the wall, even if you think you know. Have a conversation with the guy who's machining, designing, or assembling the mold. You don't want him telling you how to do sketches, so you don't tell him how to achieve what the project needs him to achieve. I always talk to the molder if I have the opportunity. It makes him happy, it makes you happy that he doesn't have to come back to you, and it makes your boss happy that the work is only done once.
Blog: http://dezignstuff.com
Re: It would be lovely...
I'm just going to have to disagree here. Either the print or the model is the master, end of story. Is there "Room for negotiation", sure, always is. But what that negotiation tells me is that who ever designed the product didn't design and dimension it properly. If you put +/-.010 on the print and "it will work" at +/-.020....then +/-.02 should have been on the print because that meets the functional need of the part.Jim Elias wrote: ↑Mon Apr 05, 2021 2:14 pmNot quite. The first thing any part manufacturer wants to know is: what is scrap and what's not scrap (i.e. what can be billed for). That's what the drawing tolerance dictates in unambiguous fashion.MJuric wrote: ↑Mon Apr 05, 2021 12:54 pmFrom a machinist point of view it is. If you give me a dimensions of 1.00 +/.01 or 1.005 +/-.005, I'm going to shoot for 1.005 in both cases. There are some exceptions to this, say dies where if this was a hole they would shoot for 1.010, because as the punch wears the hole will get smaller.
The only way to get "Closer" to a dimension is by making the tolerance tighter.
There is room to negotiate after that without needing to make that tolerance tighter. It may be that assembly requires less individual fitting if the actual tends toward limit rather than mid-tolerance, etc. But those are things that really merit detailed discussions covering both the commercial and technical aspects of the doing, and the results of those discussions belong on the work order or PO rather than the drawing.
That being said there are PLENTY of sectors where there is next to zero "Room for negotiation. I've worked on a number of aerospace projects where even if there was something discovered on the print that was patently ridiculous you had to meet the spec. Getting the print changed took an act of congress and if your inspection report did not show that the part met 100% of the specification the part was scrapped, rejected or sent back to you for rework. On some rare occasions you could submit deviations but often those were rejected as well and always went against your supplier record. Ask for too many and you're out the door.
I'm just not a believer that somehow prints are "Suggestions" and that the true need for the part is determined by purchasing and manufacturing. I think this is simply the lazy mentality created by a severe lack of talented designers that have a solid grasp on tolerances and manufacturing processes. If I'm lazily putting "Negotiable" tolerance on the parts that is unquestionably costing the company money because many, most even, wont come back to "Negotiate". Most will quote it at what it takes to meet the tolerance on the print.
For the most part I agree. Design to nominal. However I think to say that somehow not designing to nominal is "Wrong" and should never be done leaves out a whole bunch of times and reasons where not designing to nominal is not only not wrong but prefered.Jim Elias wrote: ↑Mon Apr 05, 2021 2:14 pmISO fits are indeed the usual exception to the "middle of tolerance" rule, although most shops will appreciate it if the ISO fits as well have been moved to middle of tolerance in the models they get for CAM. (There are plenty of macros out there for this.) Even so, I now avoid using/citing them in cases where there isn't a long-standing historical precedent for a defined use case, such as H7 being a transition fit for a metric dowel pin. A tolerance I choose may be identical to 40G7, but on my drawing it will say 40.025/40.009, and although I generally agree with the "clean round numbers" principle during the designing, the final archived model after the job is finished will have 40.017. It used to be that machinists and designers could immediately visualize the approximate tolerance field based on the designation, and it's just not that way any more.MJuric wrote: ↑Mon Apr 05, 2021 12:54 pm
Now that being said what do you design for features that are either "MAX" or "MIN"? If I have a .060R "MIN" inner radius, what should I model that too? It can be no smaller than .06 but I don't care if it's 2.000 or 200.
All that being said I do not think that not using "Nominal all the time in all situations" is necessary or even good design practice in some cases. I think this is particularly true in situations where you have standard fits and tolerances. If I'm going to call out an H6 fit on a hole I'm not including half the tolerance to the model because the H6 fit is -0/+X. Almost all the tolerances in the ISO system are unidirectional. Many are even +/+ and -/-. This is done this way for the express purpose that most people don't design to nominal, so that the numbers are rounded.
I can model a 40mm hole and put G7 tolerance on it and it's +.009mm/+.025mm. I don't model to 40.017mm for several reason. First you would then have to modify the dim in order to get it to read 40mm in order to get the right fit and second you're far less likely to screw up when designing around 40mm then you are when you are designing around 40.017. Clean round numbers work best for a number of reasons.
From the programming side, yep, its way easier to work with a model that is nominal, but working toward the nominal from a unilateral is not all that difficult in most cases.
Re: It would be lovely...
Matt, consulting with the actual process owner, the mold maker in this case, is exactly the point. Thank you for elucidating! (Word of the day there?) Unless we are the "owner" of the process, unless we are the ones that will actually execute the manufacture of the part, there is always someone more knowledgeable.matt wrote: ↑Mon Apr 05, 2021 2:33 pmYou know, in theory, of course, you're right. But I'm a pretty experienced plastics design guy, and when it's not really obvious, I do leave it to the mold guys. Especially if there is a core pull or something, and the mating surfaces aren't called out on a drawing. Generally, I consult with the mold maker and then model the draft explicitly, but as a plastic part designer, I'm not going to tell the molder how to design his mold. There are all sorts of things plastic part designers don't think about that the mold maker needs to determine:DennisD wrote: ↑Mon Apr 05, 2021 2:01 pm I had a junior engineer that was too arrogant and lazy to avail himself of the machine shop just outside our area. In reviewing one of his models I immediately saw things that just weren't going to fly. It was a plastic part but it straight sides and sharp corners and was modeled more like a simple machined part. I asked him about the draft and he said "Oh, I'm leaving that up to the mold maker." Okay, how about the parting line, where will that be? "Oh, I'm leaving that up to the mold maker too." Uh-huh. Where will the gate go? "What's that?" I asked if I could use his mouse for a few minutes and then quickly put in some draft, which naturally also determined the parting line. I put in a pocket for the gate and added some radii where it would be. His jaw just dropped and he said "That won't work with the other parts!" But he quickly realized it was his error in not knowing about these things.
The moral of this story is "You have to understand the process you are inherently specifying or else you are nothing more than a cartoonist." Okay, a 3-D cartoonist.
- how to get the part out of the mold.
- which side does the part stick to
- knit lines on cosmetic surfaces
- knife edges in the mold
- ejector pins
- mold cooling
- bubbler pins inserts
Otherwise, I'd be designing collapsing cores for every part because I can. Or overmolds because they're easy. Or specify structural foam process because it allows me thick walls or one of a couple dozen other mistakes that rookies who don't think they're rookies make that a mold designer doesn't make. He knows which parts are expensive or hard to machine or wear out fast, or a part that's in this catalogue but not that one.
There's nothing quite as miserable as removing draft and fillets and then redoing them with the correct scheme.
It's so easy for a plastics designer to double the cost of the mold just by not knowing that the shrink will pull away from some surfaces but on to others. Or that you might be able to allow a thick section with a bubbler, but is that really possible where you want it?
Don't throw it over the wall, even if you think you know. Have a conversation with the guy who's machining, designing, or assembling the mold. You don't want him telling you how to do sketches, so you don't tell him how to achieve what the project needs him to achieve. I always talk to the molder if I have the opportunity. It makes him happy, it makes you happy that he doesn't have to come back to you, and it makes your boss happy that the work is only done once.
I had/have a statement above the title block in the last companies where I ran the engineering departments and now with my own consulting: "The vendor is encouraged to suggest ways to improve the manufacturability of this part. Please contact the Engineering Department at (my direct number) with your requests/suggestions." I made sure we fully considered the manufacturing capabilities/limitations and we rarely had any vendor contact us, however, they often would bring that statement up in our meetings and how much they appreciated it.
I liked to sit down with my vendors, especially ones that were not close to us and we weren't as well versed as with others. I would ask them these questions:
1. What is run-of-the-mill that you are doing for others that we are not taking advantage of?
2. What are more advanced things that you are doing?
3. What is the state of the art in your industry and where are you with respect to it?
Of course these are very open questions, but it went a long way to building a great relationship and rapidly advancing our achievements. I had one particular conversation with the president and his head of engineering for a powdered metal company. When I was asking these questions on the last one I modified it a bit: "What is the state of the art in your industry and where are you with respect to it? And if you really want to make my day you can tell me you have side-action P/M." I was sitting next to the head of engineering and across from the president who said, "Dennis, the reason Adam is smiling so big is because he's about to make your day!" It was an exciting meeting because we were among the first to take advantage of this very new and very beneficial technique. And that came from our investing in learning about what was possible and striving for legitimate ways to achieve more. That process inherently evolved our vendor base.
With all our parts we routinely review them with our preferred vendors prior to release. Most of the time they do not have any big changes to recommend, but we all come out with a lot more peace of mind. However, there are those times when they point something out that is a big improvement and EVERYONE is happy. Usually the big suggestions are either for utilizing techniques that are new to the industry or new to their shop, or the suggestions are from a Design For Manufacturability/Assembly (DFMA) perspective that we overlooked. It's a win-win.
Dirty Harry has it right: "A man's got to know his limitations."
Brick walls are there for a reason. The brick walls aren't there to keep us out. The brick walls are there to show us how badly we want things.
- - -Randy Pausch
- - -Randy Pausch
Re: It would be lovely...
Most of the products I design require some hand-fitting (alignment of optical elements, etc.) during assembly, and how much fitting effort is acceptable, is ultimately decided at some upper business level. What I need to specify as a designer is is the deviation extreme beyond which the part cannot function irrespective of the effort put into assembly.MJuric wrote: ↑Mon Apr 05, 2021 2:47 pm
I'm just not a believer that somehow prints are "Suggestions" and that the true need for the part is determined by purchasing and manufacturing. I think this is simply the lazy mentality created by a severe lack of talented designers that have a solid grasp on tolerances and manufacturing processes. If I'm lazily putting "Negotiable" tolerance on the parts that is unquestionably costing the company money because many, most even, wont come back to "Negotiate". Most will quote it at what it takes to meet the tolerance on the print.
So for example, I know that 1.005" +/-0.005" will work and specify such; and then after discussion and design review with the head of assembly, we say at 1.008", you'll likely have 1 hour of fitting, and at 1.005", you'll have 2 hours of fitting, and at 1.002", you'll have 3 hours of fitting. The client may indeed choose to tighten the drawing tolerance, or choose to pay a premium for parts closer to 1.008", while accepting all parts within the original tolerance -- I've seen it both ways. That's not letting purchasing determine the technical requirements, it's giving the business owner the information needed for an informed financial decision. Component cost is only one part of the mix.
I have seen way too many expensive downstream errors due to one-sided tolerancing not being reflected in 3D -- about the same as with overridden dimensions, hence my initial comparison. Ok, design to round numbers (for ISO fits, those are the nominals) is fine, but archive for future work at middle of tolerance. It's simply clearer for anyone coming afterwards.
Re: It would be lovely...
What you're describing is, in my opinion, still part of the design process. "What fits the function" must always include price and that decision should be made at the design phase and not by purchasing or manufacturing. We do the same thing here with every machine we make. Most machines need to be aligned and need some sort of fitting spacers. How big we make them to start with will determine how much material must come off of them, which equals time and money. If I'm fitting a spindle that I know should only be +/-.06 or so off max and I leave 1/2" extra on the spacer "Just to be safe" well then I've just wasted a whole lot of money.Jim Elias wrote: ↑Mon Apr 05, 2021 3:47 pmMost of the products I design require some hand-fitting (alignment of optical elements, etc.) during assembly, and how much fitting effort is acceptable, is ultimately decided at some upper business level. What I need to specify as a designer is is the deviation extreme beyond which the part cannot function irrespective of the effort put into assembly.MJuric wrote: ↑Mon Apr 05, 2021 2:47 pm
I'm just not a believer that somehow prints are "Suggestions" and that the true need for the part is determined by purchasing and manufacturing. I think this is simply the lazy mentality created by a severe lack of talented designers that have a solid grasp on tolerances and manufacturing processes. If I'm lazily putting "Negotiable" tolerance on the parts that is unquestionably costing the company money because many, most even, wont come back to "Negotiate". Most will quote it at what it takes to meet the tolerance on the print.
So for example, I know that 1.005" +/-0.005" will work and specify such; and then after discussion and design review with the head of assembly, we say at 1.008", you'll likely have 1 hour of fitting, and at 1.005", you'll have 2 hours of fitting, and at 1.002", you'll have 3 hours of fitting. The client may indeed choose to tighten the drawing tolerance, or choose to pay a premium for parts closer to 1.008", while accepting all parts within the original tolerance -- I've seen it both ways. That's not letting purchasing determine the technical requirements, it's giving the business owner the information needed for an informed financial decision. Component cost is only one part of the mix.
What I'm talking about is the continual thing I see where someone blows a dimension and comes to engineering and says "Will this work" and the engineer doesn't even need to look at anything and says "I'm sure it will"....that shouldn't happen.
Just curious as to what errors you end up seeing? If manufacturing is blowing dimensions because they aren't paying attention to tolerances, that's hardly a reason to change ones design practices. On the other hand if someone is designing something where unilateral geometry might cause a problem with the design, one would think that in that case unilateral geometry was an inappropriate choice.Jim Elias wrote: ↑Mon Apr 05, 2021 3:47 pmI have seen way too many expensive downstream errors due to one-sided tolerancing not being reflected in 3D -- about the same as with overridden dimensions, hence my initial comparison. Ok, design to round numbers (for ISO fits, those are the nominals) is fine, but archive for future work at middle of tolerance. It's simply clearer for anyone coming afterwards.
Neither of these are reasons to say "Never use unilateral dimensions, at least in my opinion. There are certainly cases where using unilateral geometry and tolerances are more than appropriate and in fact in some cases doing it another way would at very least end up being more difficult at worst incorrect.
On the other hand there has never been a place that I can think of where manual dimensioning is appropriate or the right thing to do.
-
- Posts: 1
- Joined: Wed Apr 21, 2021 2:52 pm
- x 3
Re: It would be lovely...
I remember a time when I was running machines and a young engineer wanted a plaque engraved with writing .03" deep, +/-.03". The crusty old machinist chucked up his best sharpie, did the sign, then sent it out the door. I laughed my @$$ off and had a beer with him after work, I learned more about the trade from those chats than I ever did apprenticing.MJuric wrote: ↑Mon Apr 05, 2021 2:47 pm *snip*
That being said there are PLENTY of sectors where there is next to zero "Room for negotiation. I've worked on a number of aerospace projects where even if there was something discovered on the print that was patently ridiculous you had to meet the spec.
*snip*
Re: It would be lovely...
And that behavior may be the reason why they will put tighter than necessary tolerances on everything from that day on.AustenP405 wrote: ↑Wed Apr 21, 2021 3:43 pm I remember a time when I was running machines and a young engineer wanted a plaque engraved with writing .03" deep, +/-.03". The crusty old machinist chucked up his best sharpie, did the sign, then sent it out the door. I laughed my @$$ off and had a beer with him after work, I learned more about the trade from those chats than I ever did apprenticing.
Either one could have picked up the phone...
- mike miller
- Posts: 878
- Joined: Fri Mar 12, 2021 3:38 pm
- Location: Michigan
- x 1070
- x 1231
- Contact:
Re: It would be lovely...
What about the egghead who specified a part with a tolerance the same as the OAL?AustenP405 wrote: ↑Wed Apr 21, 2021 3:43 pm I remember a time when I was running machines and a young engineer wanted a plaque engraved with writing .03" deep, +/-.03". The crusty old machinist chucked up his best sharpie, did the sign, then sent it out the door. I laughed my @$$ off and had a beer with him after work, I learned more about the trade from those chats than I ever did apprenticing.
The machinist sent him a box of chips......


He that finds his life will lose it, and he who loses his life for [Christ's] sake will find it. Matt. 10:39
- DanPihlaja
- Posts: 842
- Joined: Thu Mar 11, 2021 9:33 am
- Location: Traverse City, MI
- x 805
- x 978
Re: It would be lovely...
Agreed. Designers and drafters make mistakes. We are human.
I am the one here who decides who we use for fixture manufacture and machining (not product machining). If a supplier sees a drawing that is missing a dimension or has a tolerance like the one described and just makes a guess and sends me back scrap instead of calling me to let me know that i might have made a mistake......then that supplier will be out of a customer.
If the machinist has to guess about something, then the designer/drafter made a mistake. If the machinist makes a guess AND CONTINUES TO MACHINE THE PART, now the mistake is squarely on the shoulders of the machinist. He should have called.
-Dan Pihlaja
Solidworks 2022 SP4
2 Corinthians 13:14
Solidworks 2022 SP4
2 Corinthians 13:14
Re: It would be lovely...
Which is a ridiculous knee jerk response to ones own error. Maybe it required tighter tolerance or maybe if should have been changed to .06 +/-.03.
Re: It would be lovely...
It has been my experience that machinist will more often than not error on the side of caution. I suspect that in this case, using a sharpie, was more of a "I'll fix him" type of thing but in the end it probably caused no damage to the part.dpihlaja wrote: ↑Thu Apr 22, 2021 9:32 am Agreed. Designers and drafters make mistakes. We are human.
I am the one here who decides who we use for fixture manufacture and machining (not product machining). If a supplier sees a drawing that is missing a dimension or has a tolerance like the one described and just makes a guess and sends me back scrap instead of calling me to let me know that i might have made a mistake......then that supplier will be out of a customer.
If the machinist has to guess about something, then the designer/drafter made a mistake. If the machinist makes a guess AND CONTINUES TO MACHINE THE PART, now the mistake is squarely on the shoulders of the machinist. He should have called.
What is more dangerous than "Guessing", which again in my experience is rare, is misinterpretation. The machinist does what they think the print is saying but the print is not really saying that. The designer however said something ambiguously or with lack of clarity and the part gets scrapped.
Re: It would be lovely...
We likely work in very different company-structural worlds. I have no dog in the part-cost vs. fitting fight (well, maybe a zero-thickness dog, but I still keep him leashed and muzzled). My job in that area is done when I submit the design summary showing more-of-this-means-less-of-that. Sometimes I even submit alternative drawings for different costing/resource planning models, and the decisions in those areas get made after I've closed out the project.
They are fully avoidable human errors. The typical one is when a designer adds a bunch of "+0.1" and "-0.1" tolerances in drafting in order to avoid having to do model tweaks... everything goes fine for awhile because it's all been NCd to middle of tolerance anyway, but for whatever reason something eventually comes out at limit, and doesn't fit anymore because the stack calculation (if done at all) contained a sign error or such. Of course, the original designer has moved on or retired by then, so no one quite knows where to start looking. Sure, tough beans and no excuses, but clients are grateful when those of us who have foresight, cushion them against such eventualities. Back in the days when CAM wasn't a given, we always dimensioned the primary NC-coordinate view with origin at the upper right corner/int, so that all coordinates were negative-signed. It was appreciated and the good word got passed on to management, designer gets on the short-list for the next gig, win-win.MJuric wrote: ↑Mon Apr 05, 2021 4:02 pm Just curious as to what errors you end up seeing? If manufacturing is blowing dimensions because they aren't paying attention to tolerances, that's hardly a reason to change ones design practices. On the other hand if someone is designing something where unilateral geometry might cause a problem with the design, one would think that in that case unilateral geometry was an inappropriate choice.
Neither of these are reasons to say "Never use unilateral dimensions, at least in my opinion. There are certainly cases where using unilateral geometry and tolerances are more than appropriate and in fact in some cases doing it another way would at very least end up being more difficult at worst incorrect.
So we'll have to agree to disagree on the general acceptability of one-sided tolerancing in the modern age. Ok, I didn't think about the times I use those clean round numbers (basically to avoid drafting messiness on fits) when I made that statement, but in general, one-sided tolerancing only adds risks because it circumvents the model, and the default attitude should thus be to question it where it is seen. Not forbid it, but do question it.
Plus (and this was actually the main point): I think it should be an imperative to deliver a 3-D reference model with the "real" dimensions (how can these ever be "incorrect"?), so that downstream designers immediately see the true airgaps and intended interference fits, and I have never experienced a CAM programmer not appreciating a fully middle-of-tolerance model. Tool radius correction is fine on an isolated feature, but model contours having varying tolerance weighting along their runs are an unkindness.
I think that how one views a comparison of an ISO fit with an overridden dimension could be a matter of degree. If a colleague gave me a drawing with a Ø5a9 shaft spec on it, I'd send it back and say please model that true. Or if you like: what is "most correct," 5a9, 4.8c9 or 4.7k9? Why then not 4.715js9? (These identical-but-different expressions all actually did imply discrete things to the dinosaur craftsfolk of yesteryear, but it's easily been 10 years since I've met a designer or shop person who knew what those would have been)
Re: It would be lovely...
I'm not going to respond line to line here but suffice it to say that there is no such thing as a hard and fast rule. If you're in an industry that for some reason unilateral dimensioning is never the best design option, then never use it.
I can say without hesitation that I have run into many applications and many reasons to use unilateral tolerancing over the years.
1) You talk about stack ups. I simply have to disagree. I've checked a lot of designs over the years and I find it WAY easier to add up a bunch of round even numbers and then deal with unilateral tolerancing than to add up a bunch of odd ball numbers and then deal with the same tolerance bands in a different place.
2) ISO tolerances are based on base numbers typically to get a certain fit. They are set up this way so at a glance you can have an idea of what the design intent is. Moving the nominal to shy away from a +/+ or -/- tolerancing completely defeats the entire purpose of the entire practice.
3) Manufacturing should not dictate how something should be designed. If I designed everything the way manufacturing wanted it to make it "Easy on manufacturing" I'd end up with a seriously degraded design. There is a big difference between "doing something stupid that makes it more difficult for manufacturing" and "Designing something correctly that is hard to manufacture". In cases where the better design is to have unilateral tolerance, that is the way it should be designed regardless of if it makes it "Harder on manufacturing"
I've seen WAY to many cases where designs were compromised to the point of being worthless because "Well it's easier if you dimension it this way for purchasing" "Oh but it should be dimensioned this way to make it easier on the welding department", "Oh and dimensioned this way for machining", " and this way for quality". Sure manufacturing may always prefer a nominal model, but of that is not the proper way to relay design intent...to bad.
I can say without hesitation that I have run into many applications and many reasons to use unilateral tolerancing over the years.
1) You talk about stack ups. I simply have to disagree. I've checked a lot of designs over the years and I find it WAY easier to add up a bunch of round even numbers and then deal with unilateral tolerancing than to add up a bunch of odd ball numbers and then deal with the same tolerance bands in a different place.
2) ISO tolerances are based on base numbers typically to get a certain fit. They are set up this way so at a glance you can have an idea of what the design intent is. Moving the nominal to shy away from a +/+ or -/- tolerancing completely defeats the entire purpose of the entire practice.
3) Manufacturing should not dictate how something should be designed. If I designed everything the way manufacturing wanted it to make it "Easy on manufacturing" I'd end up with a seriously degraded design. There is a big difference between "doing something stupid that makes it more difficult for manufacturing" and "Designing something correctly that is hard to manufacture". In cases where the better design is to have unilateral tolerance, that is the way it should be designed regardless of if it makes it "Harder on manufacturing"
I've seen WAY to many cases where designs were compromised to the point of being worthless because "Well it's easier if you dimension it this way for purchasing" "Oh but it should be dimensioned this way to make it easier on the welding department", "Oh and dimensioned this way for machining", " and this way for quality". Sure manufacturing may always prefer a nominal model, but of that is not the proper way to relay design intent...to bad.
- CarrieIves
- Posts: 163
- Joined: Fri Mar 19, 2021 11:19 am
- Location: Richardson, TX
- x 376
- x 136
Re: It would be lovely...
This is related to the asymmetric tolerances discussions. I have been designing a lot of plastic parts lately. They build the tool off the model, so it should be modeled to what you want. Reality, is that sometimes the part off the tool ends up outside the tolerances but it can still work. (Sometimes it was something that could have been wider tolerances to start, sometimes the mating part can compensate. Sometimes, it is accepting a cosmetic issue where the part edges don't line up as well, but the issue is accepted rather than taking the time to fix the tool. Schedule being the most important thing for the project at that time.) I have widened my tolerances so that parts off the tool would not be rejected because they were outside tolerances, but if the tool gets rebuilt from the model, it will be at what the nominal was supposed to be.
- Roasted By John
- Posts: 366
- Joined: Mon Mar 08, 2021 3:21 pm
- Location: Lebanon PA USA
- x 268
- x 583
- Contact:
Re: It would be lovely...
That can be a good practice, but my argument is that if the part is designed and modeled right on the dimensions etc, then it's up to the machine operator or fabricator to understand their limits, you can open a pretty largeTony Tieuli wrote: ↑Thu Mar 11, 2021 11:52 am That's an excellent start!
One thing I would add right off the top of my head is to dimension your model to the mean of the tolerance. Most CAM programmers who use the model, create their toolpaths right on the model. If the dimension is 1.000 +.010 / -.000, model it at 1.005. When you model it to the high or low the CAM programmer has to make changes to get the toolpath on the mean. Yes, you can have the machinist on the shop floor use offsets to get the part on the mean but I prefer to give them a clean program.
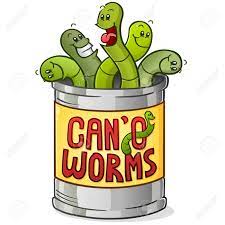
Pretty much the same thing here, we always modeled the part right on and then the shop knew what they needed to do to match the tolerances etc, since we were bought by Wyrmwood and parts started to come from their facility to ours for final finish and assembly, the parts came here way out of tolerance, now they want drawings for every step of the way, min/max on the raw material, min/max off the machines etc, this just again opens up a bigger
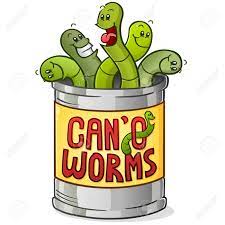
www.martinsroastapig.com
Pig Roast Your Way
Pig Roast Your Way
- Tim R. Halvorsen
- Posts: 16
- Joined: Mon May 10, 2021 7:26 am
- x 4
- x 10
Re: It would be lovely...
Assuming we are talking SOLIDWORKS CAD/CAM here....
It is pretty easy to get the first steps taken care of using Express software already available in SOLIDWORKS.
DFMXpress will look at a few common parameters for errors directly in the UI, so the engineer can check hole diameter/depth ratio easily - or holes in a sheet metal part/distance to edge ratio.
If this works as a start, then DFM has a pro solution with a LOT more settings - available for different CAD systems as well.
For modelling the parts to mean dimensions - don't.....
Just use SOLIDWORKS CAM MBD and let the CAM software read the tolerance, and machine to the mean automatically.
So we have two pieces of software taking care of everything discussed here, and they both automate the cumbersome processes.
I still very much agree that part of the education to take on a CAD design job, is 3 months running jobs in the machine shop, to understand WHY a 10xDiameter hole could be expensive, and WHY we do not need extreme geometric tolerances to make the part LOOK good.
Tim
It is pretty easy to get the first steps taken care of using Express software already available in SOLIDWORKS.
DFMXpress will look at a few common parameters for errors directly in the UI, so the engineer can check hole diameter/depth ratio easily - or holes in a sheet metal part/distance to edge ratio.
If this works as a start, then DFM has a pro solution with a LOT more settings - available for different CAD systems as well.
For modelling the parts to mean dimensions - don't.....
Just use SOLIDWORKS CAM MBD and let the CAM software read the tolerance, and machine to the mean automatically.
So we have two pieces of software taking care of everything discussed here, and they both automate the cumbersome processes.
I still very much agree that part of the education to take on a CAD design job, is 3 months running jobs in the machine shop, to understand WHY a 10xDiameter hole could be expensive, and WHY we do not need extreme geometric tolerances to make the part LOOK good.
Tim
Re: It would be lovely...
Could I start a " what are you machining today" thread?
I have a few I can share.
I have a few I can share.
- zxys001
- Posts: 1077
- Joined: Fri Apr 02, 2021 10:08 am
- Location: Scotts Valley, Ca.
- x 2304
- x 997
- Contact:
Re: It would be lovely...
I'm in for watching!... (weird, with this covid thing, I miss visiting shops and watching stuff get cut!?)

"Democracies aren't overthrown; they're given away." -George Lucas
“We only protect what we love, we only love what we understand, and we only understand what we are taught.” - Jacques Cousteau
“We only protect what we love, we only love what we understand, and we only understand what we are taught.” - Jacques Cousteau
Re: It would be lovely...
That would be cool. I always like to see what other people are doing. I can probably find some video's of machines we've built of which we machine most of the parts for. I'll have to walk around and see if we have anything interesting on any of the machines or in inspection.
Re: It would be lovely...
Sorry that would be 1\16 rad or .0625 rad
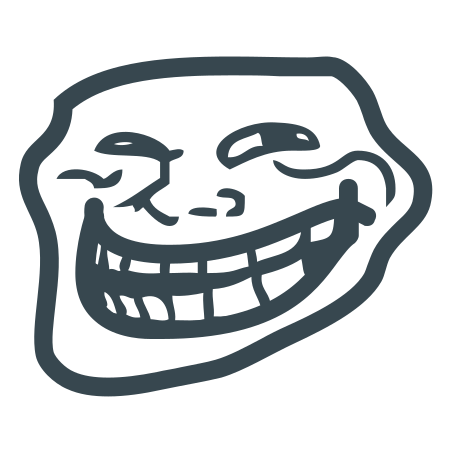